The Future of Manufacturing: All About Digital Factory
The world is moving from standard paper-based practices to a more digital and virtual world. Where everything is automated and managing data is quite simple. Similarly, the transformation from traditional manufacturing to connected and digital manufacturing is digital factory. There are many technologies that are already helping organizations to shift from paper-based data entries to digital data entries. So, what really is digital factory and what are the technologies that help a traditional factory become digitized?
Keep on reading to learn everything about a digital factory and the future of manufacturing when the world is now shifting to digital solutions.
What is a Digital Factory?
Digital factory is simply the transformation from traditional manufacturing practices to advanced practices which include an interconnected and intelligent system. This type of factory includes machines and equipment that can self-optimize, make independent decision, and can self-adapt to the changes being made. These type of machines and equipment work by using advanced technologies.
The transformation from traditional to smart manufacturing is not only about applying latest technologies in your organization. But it is about changing your workflows, processes and management philosophy. Smart factories are great when we need skills that can help us to change according to the market demands, deliver personalized goods, and when we must manage our resources and tasks efficiently.
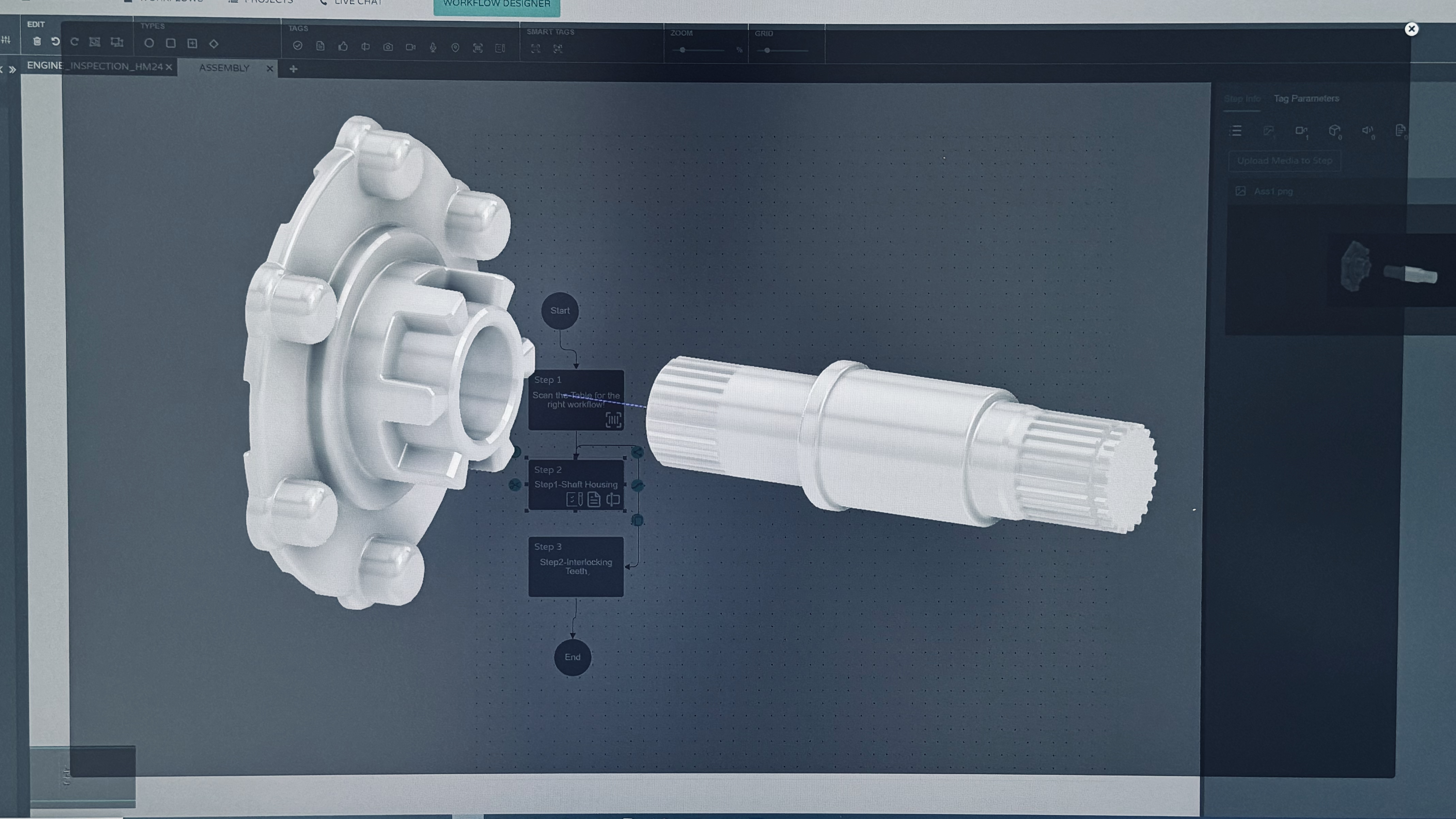
The Pillars of Digital Factory
The digital factory or smart manufacturing, both have multiple foundational pillars on which they stand. Each feature offers their own benefits and are used for integration of different functions. These include:
- IT and OT Integration: IT and OT integration includes both software and hardware. These form a backbone of the digital factory which helps in effective communication within the organization and efficient control over the operations.
- Automation and Robotics: Inclusion of automation and robotics helps with improving efficiency and minimizing human errors. The more the tasks and processes are automated, the more productive will be the assembly line and the products produce will be of high quality as there will be less errors.
- Data Analytics: Data analytics are important for any organization as they are the basis for predictive maintenance, helps in making informed decisions, continuously improve the production line, and helps in optimizing the tasks and processes.
- Digital Twin and Cyber-Physical Systems: Digital twin and cyber-physical systems offer a mix between physical and digital technologies. They produce interconnected systems which monitor and control physical processes. This helps in optimizing the workflows and increasing efficiency.
- Cloud Computing and IoT: Organizations these days need real-time data documenting. Therefore, cloud computing and IoT are essential as they help in real-time data processing and global connectivity. These allow organizations to monitor and control the manufacturing processes.
Benefits of Transitioning to a Digital Factory
If organizations shift to Digital Factory model, then they can have many benefits of the current manufacturing trends. These include:
- Increased Operational Efficiency: If IoT, AI, machine learning, and AI are implemented in the industries then it helps in optimizing and simplifying the processes. They also help in reducing the downtime, improves productivity, and maximizes the output.
- Enhanced Product Quality: If digital twins, real-time documentation, AI-driven quality control systems, and AR are included in the workflows. They provide higher accuracy and makes sure that the product quality is consistent and up to the standard.
- Production Customization and Flexibility: If modern technologies are implemented on the production line, then they allow organizations to have greater flexibility in design and production. This helps with customer satisfaction as the customers’ demands are fulfilled in such a setting.
- Sustainability: If resources are management effectively then they help in reducing waste and extra energy consumptions in the industry. For example, if cloud connectivity and big data analytics are incorporated in the workflow, they help in optimizing the resource utilization. This helps in minimizing the costs and allows industries to save energy moving towards a more sustainable organization.
- Improved Safety and Compliance: If augmented reality, predictive analytics, and advanced monitoring technologies are combined then they help in making the workstations safer and help workers to follow standards without any difficulty.
The Four Evolutionary Stages of Smart Factories
To become a Digital Factory, each organization must go through four stages. Then only they can enter the competitive global market of smart manufacturing. The stages included are:
Level One: Basic Data Collection
This is the basic level where industries start to digitize their data. The digitized data here is accessible but not completely available for use. At this stage only data collection is done from multiple resources such as machines, workers, and inventory. This level only includes digital work instructions which means shifting from paper-based records to digital records. This lays the foundation for the Digital Factory and records the data in a way that it can be used further.
Level Two: Proactive Data Analysis
At level two, the industries not only just collect data in a digital manner but also begin analysing the data in real-time. This level includes basic analysis of the data so that workers and the organization can understand the production trends, possible bottlenecks in the line, and equipment efficiency. This level helps the industries to move a step further towards decision making based on the data recorded. This is the stage where processes and tasks are optimized using the workflow insights.
Level Three: Real-Time Data Utilization
The third level is where the organizations do not just analyse the data but also use it in real-time to complete tasks and processes. In this stage integration of IoT and cloud computing are done. They allow live monitoring and adjustments in the workflow. This level is all about dynamic task management, and response. Here, just like digital work instructions, the data is recorded in real-time, and it allows organizations to make informed decisions and guide operational processes, so the assembly line works smoothly.
Level Four: Predictive Data for Autonomous Decision-Making
This is the last level where organizations become fully interconnected with the smart technologies and environments. The data and information being recorded in real-time is not used just for insights but also for independent actions. The advanced artificial intelligence algorithms use that data to predict issues and generate solutions for them without any human interference. This leads to self-optimizing and highly efficient and productive manufacturing setting.
Summary
Can we imagine an industry where technology not only assists but increase the human potential? The part to digital factory is a journey of evolution, it is important for any industrial sectors progress. A smart factory showcases a perfect blend between advanced technology and workforce which helps in improving efficiency, quality, and innovation.
Smart factories are playing a more and bigger role in changing the production industries as technologies like machine learning, artificial intelligence, blockchain, augmented reality, and internet of things develop. This change is not only about staying ahead in the competition but also changing the industrial sector for the upcoming generation.