Typical Applications Of Digital Work Instructions
Digital work instructions (DWIs) are changing the way our industries work as they are helping in providing clear, and interactive guidance to workers through different digital devices. These instructions are different than your typical paper written instructions and are particularly beneficial for manufacturing, maintaining, and quality assurance processes. In this article, we will view the typical applications of digital work instructions, focusing on their use with smartphone (both iOS, and Android), and smart glasses like RealWear. So, let’s learn more about where these instructions can be incorporated for efficient and smooth workflows.
1- Manufacturing
The first industry on the list is the manufacturing industry. As we discussed, the DWIs are beneficial particularly for quality assurance, maintenance, and manufacturing, the Manufacturing sectors has all these elements to look out for. Here we see how DWIs can be beneficial for assembly lines, quality control, and keeping your workers trained, onboard and updated with all the technologies and processes used in the specific manufacturing industry.
Assembly Lines
When it comes to assembly lines, the digital work instructions are beneficial as they provide step-by-step guidance. They provide detailed and automated step-by-step instructions for assembling products. This way the errors in the assembly can be reduced while improving the efficiency of the assembly line. The digital instructions are not just simple written texts but include images, videos, diagrams, etc. which helps in improving the understanding of the complex assembly processes or designs. This in turn helps the workers to always have the latest information and to perform tasks without skipping or forgetting a step. The digital work instructions provide real-time updates which instantly show the change in the production line or product design. Providing workers with real-time instructions so that the tasks are performed accurately without having any bottlenecks.
Quality Control
To control the quality of the products being made in the manufacturing industries, digital work instructions are the best tool to use. They help in inspection procedures, data collection, and feedback incorporations for the workflow. The DWIs guide the worker through standardized inspection steps, making sure that there is consistency and accuracy in the production. Then workers can record the inspection results directly on their smart devices. This helps in keeping the results up-to-date and simplifying data collection and analysis. Similarly, through DWIs we can get real-time feedback which allows workers to report issues instantly. Allowing quick solutions and continuous improvement in production.
Training and Onboarding
To train the workers and keep them on board with all the information in the industry, digital work instructions can be utilized. They can be used as interactive training modules and provide consistent training to the workers. In such a case DWIs work as effective training tools that help new workers to understand and perform tasks efficiently. Also, standardized digital work instructions make sure that each worker gets the same quality of training. This helps in reducing variability in performance of workers and increases the efficiency of the workflow.
2- Maintenance and Repairs
The second industry on the list is the maintenance and repair industry. For maintenance and repair industry schedules are important as well as real-time troubleshooting and repairs. Both tasks can be accomplished through digital work instructions. Here is how:
Scheduled Maintenance
With the automatic scheduling system, the digital work instructions provide detailed schedules and instructions to workers. These include instructions for routine maintenance tasks, which helps in performing all the tasks correctly and on time. The digital verification and checklists help with making sure that all the steps are completed and verified. This reduces the risk of mistakes in the workflow. Devices like RealWear can connect to IoT sensors, this is useful for getting real-time data on equipment stations and benefits by guiding workers through maintenance processes based on the current conditions.
Troubleshooting and Repairs
For troubleshooting and repairs, the digital work instructions can be used for diagnostic procedures, access to manuals, and remote assistance. DWIs can guide workers through systematic troubleshooting to identify and resolve problems or errors quickly. The workers can also access detailed manuals and repair guides directly on their devices. This reduces the extra time taken to search for paper documents. Devices like RealWear, and your smartphones, enable remote professionals to provide rea-time assistance annotation. While guiding workers to perform complex repairs via live video or audio call.
3- Field Services
The third industry on the list is field services. They mainly focus on customer support, installation, and setups. By implementing DWIs in field services consistency, accuracy, customer satisfaction, and more can be improved. Let’s have a look at each application separately.
Installation and Setup
The digital work instructions provide detailed and step-by-step instructions for installing and setting up equipment at customer sites. The workers can easily use them remotely to install and set up equipment, ensuring consistency and accuracy in the installation of tools. The digital checklists allow tracking of completion of all the compliance and safety checks during the installations on site.
Customer Support
With the help of DWIs, the field service technicians can easily troubleshoot and resolve customer issues efficiently. This reduces downtime and enhances customer satisfaction. They can also directly document their work on the devices. This makes recording of the service calls and repairs accurate and easy.
4- Warehouse and Inventory Management
The fourth on the list is the warehouse and inventory management sector. Here, inventory tracking, order picking, receiving, and inspection can all be handled smoothly through digital workstations. Let’s discuss each one separately.
Inventory Tracking
When it comes to inventory tracking, there are two main tasks to be performed. The first is barcode scanning, and the other is real-time updates which can easily be performed through DWIs. The digital work instructions integrate with barcode scanning capabilities which can be done through their smartphone cameras, RealWear glasses cameras, or any other camera that is synchronized with the system. This type of scanning helps the workers to track the inventory efficiently and accurately. The inventory is updated in real-time, which enables accurate stock management and decreases the risk of shortages or overstocking.
Order Picking
In order picking, digital work instructions help in guided picking and efficient tracking of products. They provide detailed instructions for picking and packing orders, which optimizes the route and reduces errors. While the data collected through the DWIs can be analyzed to track the picking efficiency. This helps with discovering areas for improvement in order picking and packing.
Receiving and Inspection
Inspection and documentation of goods is now quite easy thanks to the advanced digital work instructions. The DWIs guide the workers through the process of receiving goods. From receiving to inspection and documentation can all be done through DWIs. The instructions also include prompt quality checks to ensure that the received goods meet the required standards, and any issues or differences can be reported immediately providing efficient workflow in minimum time.
5- Healthcare and Pharmaceuticals
The last industry to benefit from the digital work instructions is our healthcare and pharmaceuticals. The workers and staff there can use DWIs for multiple purposes such as equipment calibration, assembly of medical devices, and pharmaceutical production.
Equipment Calibration
Easy data logging and calibration of equipment can be done through DWIs. These digitized work instructions provide detailed instructions to calibrate any type of medical equipment. You just must select or scan the equipment that you are using, and you can set up and calibrate it in just a few minutes on your own. This ensures accuracy and compliance with regulatory standards. This can further help is automatic logging of data into the system which makes it easy to gather a reliable record for audits and inspections.
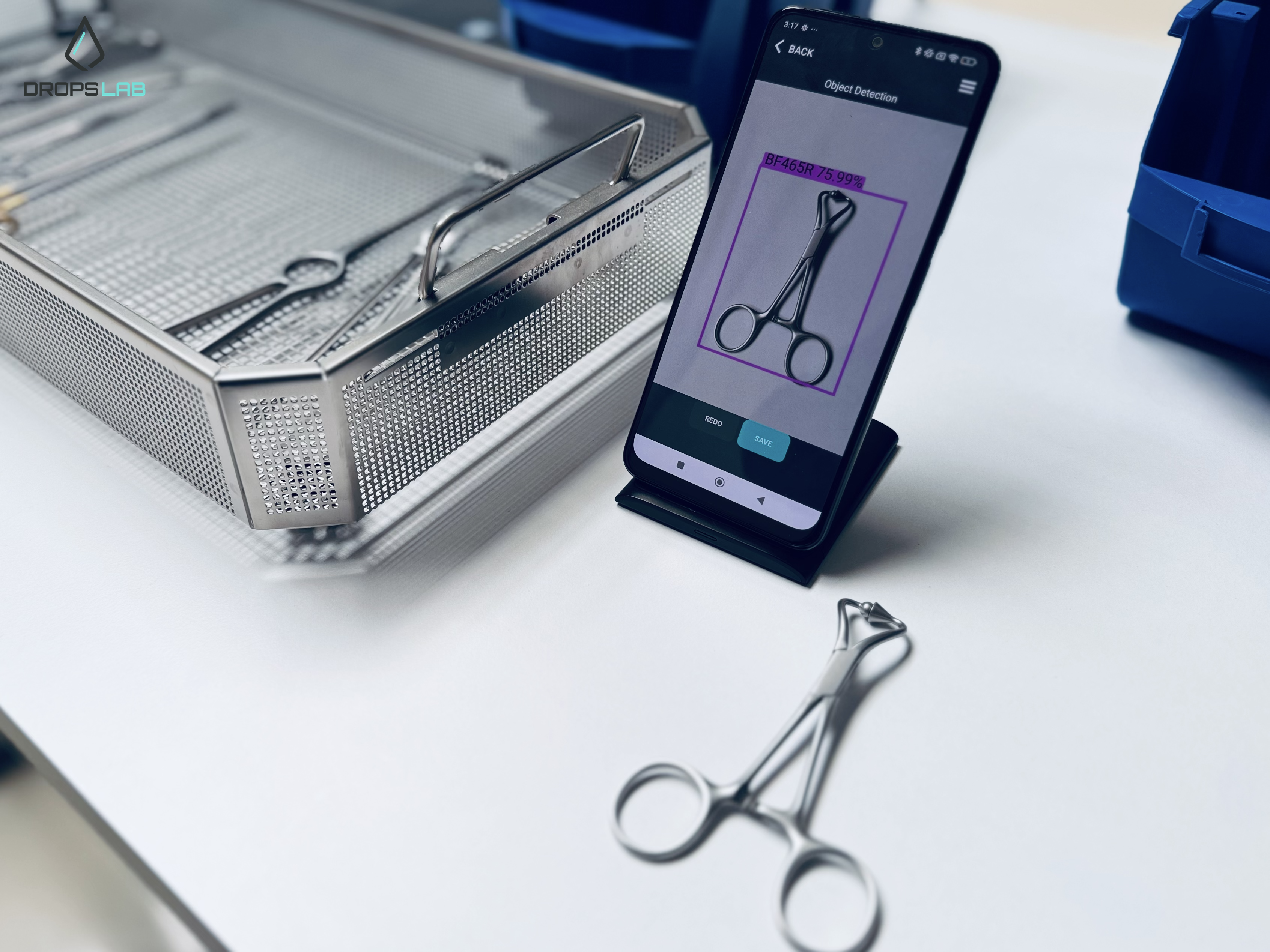
Assembly of Medical Devices
Remembering steps to assemble medical devices is quite hard especially if you are new to work. In such a case, digital work instructions come in handy as they ensure the precise assembly of medical devices in a short time. This reduces the risk of defects or wrong assembly. The DWIs are updated in real-time to show the changes in regulatory requirements which ensures continuous compliance.
Pharmaceutical Manufacturing
The batch processing workers and documenters can benefit from DWIs. These instructions provide step-by-step guidance to workers through difficult batch processing steps, making sure that the processing is done consistently and follows the protocols. These digitized instructions help with detailed record keeping for each batch which helps in traceability and alignment with industry standards.
Final Words
The digital work instructions are a new means of storing your manuals, and other industry-related data. They are transforming multiple industries by providing real-time, and interactive guidance to workers. From manufacturing to field service and healthcare, these instructions provide improved accuracy, efficiency, and uniformity. By using devices like your smartphone with software using DWIs, and RealWear, companies can ensure that workers have access to up-to-date information, visual aids, and interactive elements that significantly enhance task execution and overall operational performance. So, connect with us today and get your DWIs and optimize your workflow management and processes.